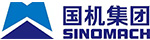
文章出處:知識中心 網(wǎng)責(zé)任編輯: 洛陽軸承 閱讀量: 發(fā)表時間:2021-10-14 11:40:43
性能試驗是輪轂軸承產(chǎn)品開發(fā)的重要環(huán)節(jié),根據(jù)輪轂軸承的功能分析了其性能要求及決定性能的因素,總結(jié)了耐久性試驗、彎曲疲勞試驗、密封試驗、高速泄漏試驗、摩擦力矩試驗、沖擊強度試驗、路肩沖擊試驗、力矩剛性試驗、微動磨損試驗及其他功能試驗方法在各大主機廠的研究進(jìn)展,評價了現(xiàn)有輪轂軸承性能試驗方法,并對相關(guān)研究進(jìn)行了展望。
伴隨汽車工業(yè)的飛速發(fā)展,行業(yè)競爭日趨激烈,對汽車零部件品質(zhì)的要求越來越高,各大主機廠加大了汽車基礎(chǔ)技術(shù)的研發(fā)投入。輪轂軸承是汽車底盤零部件中的安全件,備受主機廠關(guān)注,為開發(fā)具有優(yōu)異性能的輪轂軸承,主機廠的科研人員不斷探索更加全面、科學(xué)、合理的試驗方法,以評價輪轂軸承的性能,為開發(fā)前端提供重要的基礎(chǔ)支撐。
輪轂軸承的性能試驗方法在全球范圍內(nèi)尚未達(dá)成共識,沒有統(tǒng)一的國際標(biāo)準(zhǔn)。各國在工業(yè)領(lǐng)域即使已形成部分輪轂軸承標(biāo)準(zhǔn),如美國汽車工業(yè)協(xié)會標(biāo)準(zhǔn)SAE、德標(biāo)工業(yè)標(biāo)準(zhǔn)DIN、日本工業(yè)標(biāo)準(zhǔn)JIS、中國機械行業(yè)標(biāo)準(zhǔn)JB等,但并沒有出臺相應(yīng)的法規(guī)進(jìn)行強制實施,基本處于參考狀態(tài),主流輪轂軸承制造商仍依從主機客戶的試驗標(biāo)準(zhǔn)執(zhí)行輪轂軸承產(chǎn)品的設(shè)計、論證與評價。
輪轂軸承性能試驗方法的研究工作主要集中在全球主流的車企,分為歐系(典型代表是大眾、寶馬、奔馳),美系(典型代表是通用、福特等),日系(典型代表是豐田、本田、馬自達(dá)等)。中國車企仍未形成自己的性能試驗方法研究體系,各大車企均在不斷地對國外試驗規(guī)范進(jìn)行借鑒、吸收與采用,也積極與輪轂軸承供應(yīng)商進(jìn)行聯(lián)合研究工作,使輪轂軸承性能試驗規(guī)范趨于合理。據(jù)不完全統(tǒng)計,全球輪轂軸承性能試驗規(guī)范達(dá)近百種,各大車企的試驗方法規(guī)范也各有優(yōu)劣,不同車企大量的車輛售后軸承召回事件與其設(shè)計評估的試驗方法不合理有很大關(guān)系。
綜上,對輪轂軸承的性能需求進(jìn)行分析,綜述當(dāng)前國際主流的輪轂軸承性能試驗方法,對比分析其合理性并提出評價概述,為國內(nèi)輪轂軸承性能試驗的研究提供參考。
1、輪轂軸承性能要求與分析
乘用車輪轂軸承在整車上發(fā)揮著承載與傳動這2大功能,對功能可靠性的滿足又衍生出相應(yīng)的性能要求:長壽命、低摩擦、高強度、高剛度、抗沖擊、耐微動、抗泄漏、抗泥水等。以典型的第三代輪轂軸承單元為例,輪轂軸承的性能要求與各基礎(chǔ)件要求之間的映射關(guān)系如圖1所示。決定輪轂軸承每個性能的因素多且復(fù)雜,全面評價輪轂軸承性能需要涉及到多種性能試驗,可歸納為10項(表1)。
圖1 輪轂軸承性能影響映射圖
Fig.1 Mapping diagram of performance effect of hub bearing
表1 輪轂軸承性能試驗項目
Tab.1 Performance test items of hub bearing
2、輪轂軸承性能試驗方法的應(yīng)用及評價
2.1 耐久性試驗方法
2.1.1 載荷譜的研究現(xiàn)狀
輪轂軸承耐久性試驗的目的是評價軸承的滾道接觸疲勞壽命,當(dāng)前耐久性試驗方法的研究核心在于編制耐久性試驗載荷譜。耐久性試驗載荷譜的研制流程如圖2所示,其編制依據(jù)為:在實車道路的行駛過程中,采用安裝于輪端的加速度傳感器、六分力傳感器或被標(biāo)定的應(yīng)變橋采集車輪承受的載荷,利用雨流計數(shù)法對載荷信息進(jìn)行分類統(tǒng)計以獲得載荷譜的雛形,借鑒輪轂軸承設(shè)計理論中的理論算法對輪端載荷進(jìn)行估算,綜合這兩者信息并適當(dāng)引入強化因子從而獲得一個標(biāo)準(zhǔn)的耐久性試驗載荷譜。
圖2 輪轂軸承耐久性試驗載荷譜的研制流程
Fig.2 Development process for durability test load spectrum of hub bearing
按照歐系、美系、日系車企的劃分,將輪轂軸承行業(yè)所采用的載荷譜歸類如下:
1)歐洲的AK45試驗,已形成了歐洲標(biāo)準(zhǔn),被大眾與奧迪采用。由于對原始道路載荷信息處理理解上的差異,奔馳進(jìn)一步在原始?xì)W洲采集譜的基礎(chǔ)上制定了AK51試驗。試驗的載荷條件相同,但大循環(huán)的載荷步驟存在差異,AK45為45個步驟,AK51為51個步驟,兩者最苛刻的步驟均為第43步,其載荷的當(dāng)量條件達(dá)到了1.0g(g為重力加速度,下同)。
2)美系典型的兩大車企為通用與福特,分別采用了20步法與2步法。20步法的制定思路更接近于歐洲的AK45,但所應(yīng)用的強化因子要遠(yuǎn)小于AK45,載荷試驗條件更加寬松;2步法為簡單的理論受力模型中+0.6g與-0.6g側(cè)向加速度條件下的試驗載荷。
3)日系車企的載荷譜制定思路相對簡單,一般采用2~4個載荷步驟,在0g,±0.3g與±0.6g之間循環(huán)試驗,與福特的載荷譜有共同之處。
對比上述載荷譜條件可知:歐系載荷譜條件最苛刻,瞬時工作應(yīng)力一般會超出4 200 MPa的最大額定靜載荷。因載荷的苛刻程度,在輪轂軸承設(shè)計上除考慮滾道接觸疲勞壽命外,必須要兼顧凸緣類結(jié)構(gòu)件的強度,甚至軸向車輪預(yù)緊的緊固件或緊固方式的設(shè)計。目前,軸承公司也制定有相應(yīng)的企業(yè)試驗標(biāo)準(zhǔn),尤其是國內(nèi)軸承公司,為滿足國內(nèi)缺乏載荷譜研究的主機客戶開發(fā)項目的需求,一般推薦將軸承公司自身的載荷譜作為滾道接觸疲勞壽命的評價方法。例如,浙江萬向精工有限公司不僅全面制定了輪轂軸承性能試驗規(guī)范企業(yè)標(biāo)準(zhǔn),也承擔(dān)研制了浙江制造輪轂軸承的地方標(biāo)準(zhǔn),同時聯(lián)合廣汽、吉利、北汽等國內(nèi)車企制定了主機客戶的試驗標(biāo)準(zhǔn)規(guī)范。
2.1.2 試驗細(xì)節(jié)的處理
1)加載模式的選定。行業(yè)內(nèi)存在旋轉(zhuǎn)件加載、非旋轉(zhuǎn)件加載這2種加載模式,從原理圖(圖3)中可看出2種加載模式在載荷傳遞上存在顯著差異:旋轉(zhuǎn)件載荷傳遞路徑為加載臂、中間支承軸承、旋轉(zhuǎn)工裝、試驗軸承的旋轉(zhuǎn)零件、試驗軸承的滾道;非旋轉(zhuǎn)件載荷傳遞路徑為加載臂、非旋轉(zhuǎn)工裝、試驗軸承的非旋轉(zhuǎn)零件、試驗軸承的滾道。旋轉(zhuǎn)件加載模式的載荷傳遞效果對整車車輪上的受力模擬更為真實,由于其引入了一個支承軸承,試驗總成的系統(tǒng)剛性比非旋轉(zhuǎn)件加載的更小,大量對比試驗表明旋轉(zhuǎn)件加載的壽命比非旋轉(zhuǎn)加載的壽命高出近1倍。在2015年之前,大眾與奧迪普遍采用旋轉(zhuǎn)件加載模式評估輪轂軸承滾道接觸疲勞壽命;在2015年后,為加速壽命試驗,更改為非旋轉(zhuǎn)件加載模式。目前,整個行業(yè)普遍采用非旋轉(zhuǎn)件加載模式開展耐久性試驗,但奔馳、馬自達(dá)仍采用旋轉(zhuǎn)件加載模式執(zhí)行耐久性試驗。
圖3 輪轂軸承耐久性試驗的加載模式
Fig.3 Loading modes for durability test of hub bearing
2)試驗載荷方向的標(biāo)定。在20世紀(jì)90年代前,汽車輪轂軸承行業(yè)未開展臺架上加載載荷方向?qū)υ囼瀴勖绊懙纳钊胙芯浚緸闄C械式地照搬借用。實際上,耐久性試驗是對車輪受載的模擬,試驗臺架上載荷方向的標(biāo)定應(yīng)與整車坐標(biāo)系中的方向定義保持一致。以圖3所示原理圖為例:當(dāng)采用旋轉(zhuǎn)件加載執(zhí)行試驗時,與整車條件一致,其加載方向也應(yīng)與車輪受力方向一致;而采用非旋轉(zhuǎn)件加載時,根據(jù)作用力與反作用力的關(guān)系,其加載方向應(yīng)與車輪受力方向相反。
3)冷卻方式的執(zhí)行。以整車在路面行駛為基準(zhǔn),輪轂軸承在此過程中不斷與外界發(fā)生熱交換,該條件在輪轂軸承耐久性試驗中應(yīng)得到模擬。在20世紀(jì)90年代前,主機客戶并未在其試驗規(guī)范中明確冷卻的執(zhí)行細(xì)則,軸承制造商在實驗室一般采用強制氣流進(jìn)行試驗全程的冷卻。近年來,通過研究輪轂軸承試驗條件對其滾道壽命的影響,發(fā)現(xiàn)輪轂軸承試驗的散熱條件對其壽命存在顯著影響。隨著對該條件研究的逐漸深入,大眾與寶馬分別制定了90 ℃與80 ℃作為冷卻執(zhí)行的臨界點,并規(guī)定冷卻氣流必須為自然風(fēng),而非強制壓縮氣流,其他德系、美系、日系車企也在該冷卻模式上逐漸達(dá)成共識。
4)工裝條件的采用。工裝條件在于對輪轂軸承安裝條件的模擬,目前也存在2種處理方法(圖4):一種是采用替代工裝連接輪轂軸承,另外一種是采用原裝轉(zhuǎn)向節(jié)或車輪支架連接輪轂軸承后再連接試驗工裝。相比替代工裝模式,采用原裝轉(zhuǎn)向節(jié)使得試驗?zāi)M條件趨于真實,降低了試驗總成剛度,具有提升試驗壽命的效果。目前,歐系車企逐漸在引入原裝轉(zhuǎn)向節(jié)或車輪支架開展試驗,而美系、日系車企仍維持替代工裝的試驗?zāi)J健?/span>
圖4 輪轂軸承耐久性試驗的工裝模式
Fig.4 Tooling modes for durability test of hub bearing
2.1.3 評判準(zhǔn)則
1)定值評判法。主機客戶根據(jù)其典型車型整車道路的壽命試驗結(jié)果確定一個定值來評判臺架壽命結(jié)果是否合格。近年來,隨著車型多樣化,整車重量、車輪半徑、車輪偏距、重心高均在發(fā)生變化,這帶來了輪轂軸承工況的變化,從而使得定值評判法的合理性飽受質(zhì)疑,逐漸被摒棄。
2)變值評判法。主機客戶將整車工況作為邊界條件輸入,由輪轂軸承制造商進(jìn)行設(shè)計計算,一般采用ISO 281壽命計算方法獲得不同車型工況條件下的理論壽命L10,評判試驗壽命應(yīng)不低于L10。該方法更合理,逐漸被各大主機客戶接受。
3)比較評判法。該方法也稱為經(jīng)驗法,通過融合定值、變值評判法進(jìn)行綜合評估,德系車企多采用該方法,在評估輪轂軸承供應(yīng)商臺架試驗壽命是否滿足定值要求的同時,選擇多家供應(yīng)商的壽命進(jìn)行對比判定。例如,對于同一個主機配套項目,開發(fā)第1家供應(yīng)商并量產(chǎn),然后開發(fā)第2家供應(yīng)商且要求其提供的軸承試驗壽命應(yīng)不低于第1家,這種方法也優(yōu)于定值評判法。
2.2 彎曲疲勞試驗方法
輪轂軸承彎曲疲勞試驗的目的是評判輪轂軸承凸緣類旋轉(zhuǎn)零件的結(jié)構(gòu)強度。目前,輪轂軸承行業(yè)存在2類試驗原理:
1)試驗軸承固定,采用彎矩載荷旋轉(zhuǎn)獲得對輪轂軸承結(jié)構(gòu)的疲勞試驗(圖5);
2)彎矩載荷固定,軸承旋轉(zhuǎn),加載原理與圖4耐久性試驗一致。第1類與第⒉類試驗的彎矩載荷M1 ,M2,分別為
式中:m為離心塊質(zhì)量;ω為離心塊旋轉(zhuǎn)角速度;r為離心塊旋轉(zhuǎn)半徑;L為加載力臂長度;Fa為軸向載荷;R為車輪半徑;Fr為徑向載荷;eT為車輪偏距。
圖5 第1類彎曲疲勞試驗原理圖
Fig.5Schematic diagram of first sort of bending fatigue test
彎曲疲勞試驗需要評價凸緣類旋轉(zhuǎn)零件的疲勞極限,試驗采用的彎矩水平均超過0.8g側(cè)向加速度下的載荷,該載荷條件下的軸承滾道接觸應(yīng)力一般達(dá)到了5 000 MPa,采用第2類彎曲疲勞試驗方法較難評估凸緣的疲勞極限,往往出現(xiàn)滾道疲勞剝落失效早于凸緣結(jié)構(gòu)疲勞裂紋失效。美系、日系、部分德系車企(如奔馳)均采用第2類彎曲疲勞試驗方法,針對滾道疲勞剝落的先發(fā)性,可按照定時截止試驗,只要滿足要求的規(guī)定壽命就終止試驗,但是難以獲得產(chǎn)品的極限壽命。
由于第2類彎曲疲勞試驗方法的局限性,大眾、奧迪、寶馬均采用第1類彎曲疲勞試驗方法。軸承不發(fā)生旋轉(zhuǎn),滾道不存在切向應(yīng)力,采用第1類彎曲疲勞試驗方法預(yù)防了滾道疲勞失效,能夠評判結(jié)構(gòu)件的裂紋。然而,與整車車輪道路運行工作特征相比,第1類彎曲疲勞試驗方法也存在一定的局限性,以第三代輪轂軸承為例:凸緣旋轉(zhuǎn),外圈零件不旋轉(zhuǎn),只有凸緣才存在彎曲疲勞的工況,而外圈零件無彎曲疲勞工況。采用第1類試驗方法,因彎曲載荷隨著離心塊360°旋轉(zhuǎn),使得輪轂軸承的凸緣及外圈零件均存在彎曲疲勞工況,這一點顯然背離了實際車輛的工況特征。在大量的主機項目開發(fā)中,率先出現(xiàn)裂紋的零件往往不是凸緣,而是外圈,實際上也并未評估出凸緣的疲勞極限壽命。
為解決以上2類彎曲疲勞試驗方法的矛盾性問題,浙江萬向精工有限公司于2016年開始研制第3類彎曲疲勞試驗方法并逐步應(yīng)用于實際產(chǎn)品的開發(fā),其核心是改進(jìn)第1類彎曲疲勞試驗方法,通過研制特種工裝摒棄輪轂軸承的外圈、內(nèi)圈與鋼球等零件,僅在試驗臺上對凸緣進(jìn)行疲勞試驗。采用第3類彎曲疲勞試驗方法的某凸緣試驗結(jié)果如圖6所示,在軸頸部探傷出裂紋,試驗效果十分理想。
圖6 第3類彎曲疲勞試驗方法失效模式
Fig.6 Failure mode of third sort of bending fatigue test method
2.3 密封試驗方法
輪轂軸承密封試驗的目的是評判輪轂軸承的密封性能。在實際車輛運行中,車輪的運行環(huán)境較為惡劣,外界的高、低溫,涉水路面,雨水,潮濕天氣均對對輪轂軸承的密封提出了高要求。為最大程度的模擬整車的運行環(huán)境,需要引入以下5類密封試驗條件:
1)載荷。主機廠均在0g與±0.3g的載荷條件中來回切換,載荷對密封試驗結(jié)果的影響主要是對試驗總成的剛度影響,過大載荷引起過大的剛度傾角,對密封唇口產(chǎn)生“打開”效果,降低試驗軸承的密封性。
2)泥漿配方。泥漿成分主要包括標(biāo)準(zhǔn)亞麗桑那粉塵、氯化鈉、氯化鈣、碳酸氫鈉、純凈水等,不同配方中各成分的占比有所差異。高比例的鹽分會增加零件的腐蝕,促進(jìn)金屬零件表面材料的腐蝕脫落,而高比例的粉塵將加劇密封唇口的磨損。
3)泥漿流量。泥漿流量過大不僅會加大泥漿參與磨損面積,還會對唇口產(chǎn)生一定的沖擊壓強。若密封唇口接觸壓力過小,易被沖開發(fā)生失效。
4)噴管。主機客戶采用的噴管數(shù)量并不統(tǒng)一,一般不少于2根,一根對準(zhǔn)內(nèi)側(cè)密封噴射,另一根對準(zhǔn)外側(cè)密封噴射;也存在采用4根噴管的情況,2根對應(yīng)內(nèi)側(cè),2根對應(yīng)外側(cè)。噴管數(shù)量越多,噴射距離越近,在同等流量下對密封的磨損越嚴(yán)重。
5)工裝條件。德系(大眾、奧迪、寶馬、奔馳)和部分日系(馬自達(dá))車企在密封試驗中引入了輪轂軸承的原裝周邊零件(制動盤、擋泥板、驅(qū)動軸、轉(zhuǎn)向節(jié)或車輪支架等)以最大程度的還原輪轂軸承的整車安裝條件,這種條件的引入使得泥漿應(yīng)用噴射中不是直接侵入密封唇口接觸區(qū)域,而是通過其他周邊零件導(dǎo)流進(jìn)入密封唇口的接觸區(qū),降低了密封失效概率。而美系(通用、福特)和其他日系車企(日產(chǎn)、豐田等)仍采用替代工裝執(zhí)行密封試驗。2種工裝條件的對比如圖7所示。
圖7 2種工裝條件下的密封試驗
Fig.7 Seal test under two kinds of tooling conditions
顯然,密封試驗除了與以上試驗條件有關(guān)外,還與試驗時長密切相關(guān),典型主機客戶的密封試驗條件及其評價見表2,其中星號越多表示試驗越苛刻。由于密封試驗的影響因素較多,為保證密封試驗的準(zhǔn)確性及可靠性,試驗中應(yīng)重點關(guān)注流量、泥漿濃度和噴管位置的均勻性,在密封試驗系統(tǒng)的開發(fā)中應(yīng)充分考慮這3點。
表2 輪轂軸承密封試驗條件對比
Tab.2 Comparison of seal test conditions of hub bearings
2.4 高速泄漏試驗方法
輪轂軸承高速泄漏試驗的目的是同時評判輪轂軸承潤滑脂的抗泄漏性與密封性。輪轂軸承的道路行駛工況國內(nèi)限速為120 km/h,一般車輪運行最高轉(zhuǎn)速不大于1 500 r/ min,但在國外路況不限速的條件下,車速可以達(dá)到200 km/h。目前,所有主機廠基本達(dá)成共識,統(tǒng)一按照2 000 r/ min的轉(zhuǎn)速執(zhí)行高速泄漏試驗,全程不對試驗軸承冷卻,連續(xù)運行24 h后停止試驗,評價潤滑脂的泄漏量,泄漏量要求控制在軸承注脂量的5%以內(nèi)。當(dāng)前國內(nèi)、外輪轂軸承供應(yīng)商的產(chǎn)品水平均能夠順利通過該項試驗。
2.5 摩擦力矩試驗方法
輪轂軸承摩擦力矩試驗的目的是評判輪轂軸承的動態(tài)摩擦水平。輪轂軸承屬于組件,在其內(nèi)部存在3類摩擦:
1)滾動體、滾道、潤滑脂三者之間的滾動摩擦;
2)滾動體、保持架、潤滑脂三者之間的滑動摩擦;
3)密封、摩擦副表面、潤滑脂三者之間的滑動摩擦。
目前,輪轂軸承摩擦力矩測量分為2類:
1)對輪轂軸承加載測量,以大眾、通用、福特、日產(chǎn)、馬自達(dá)為代表;
2)對輪轂軸承不加載測量,以寶馬、奔馳、本田為代表。加載與不加載對軸承內(nèi)部鋼球上的載荷分布以及密封唇口的接觸壓力產(chǎn)生的影響不一樣,測量結(jié)果也存在差異。
加載測量輪轂軸承摩擦力矩是一大技術(shù)難點,洛陽軸承研究所有限公司在2005年開發(fā)了機械支承軸承實現(xiàn)加載狀態(tài)下摩擦力矩的測量,由于機械支承軸承引入的額外摩擦,降低了摩擦力矩測量精度。2014年,國內(nèi)以萬向精工為代表開發(fā)了氣浮加載模塊,氣體摩擦因數(shù)降低到了0.000 01,基本消除了外部摩擦的影響,提升了摩擦力矩的測量精度和穩(wěn)定性,其加載模塊的原理如圖8所示。
圖8 摩擦力矩氣動加載模塊原理圖
Fig.8 Schematic diagram of friction torque pneumatic loading module
大眾與奧迪在2018年聯(lián)合出臺了PV8607摩擦力矩測試規(guī)范,提出了對NEDC譜與WLTC譜的運行摩擦能耗和平均摩擦力矩測量要求。為執(zhí)行該規(guī)范,德國布倫瑞克大學(xué)與Sincotec公司均開發(fā)出了以液浮軸承為支承,引入環(huán)境箱模塊,能夠?qū)崿F(xiàn)加載、不同環(huán)境溫度、正反轉(zhuǎn)這3種條件下摩擦力矩的測量。
隨著新能源汽車的逐漸普及,各大主機廠均在評估汽車零部件的能耗,當(dāng)前所有主機廠通過摩擦力矩對輪轂軸承能耗的評估均為短期評估,而非產(chǎn)品的全生命周期評估,無法替代軸承全生命周期內(nèi)的能耗。全生命周期軸承能耗的影響因素多且非線性,包括滾道磨損、潤滑惡化以及密封磨損與老化。采用扭矩傳感器對一套第三代輪轂軸承在臺架壽命試驗中的全程摩擦力矩進(jìn)行跟蹤測量,結(jié)果如圖9所示,顯然采用當(dāng)前的短期摩擦能耗測量難以避免以偏概全的問題。
圖9 第三代輪轂軸承壽命試驗中的摩擦力矩跟蹤測量
Fig.9 Friction torque tracking measurement during life test of thirdgeneration hub bearing
2.6 沖擊強度試驗方法
輪轂軸承沖擊強度試驗的目的是評判輪轂軸承結(jié)構(gòu)件的抗沖擊強度。輪轂軸承沖擊強度試驗方法基本完全沿用了鋁合金輪轂的沖擊試驗標(biāo)準(zhǔn)SAE J175,對應(yīng)的國標(biāo)為GB/T15704——2005雖然該標(biāo)準(zhǔn)是為輪轂制定的,但經(jīng)過不斷地摸索驗證,發(fā)現(xiàn)其對輪轂軸承評估的意義不亞于輪轂。應(yīng)用研究發(fā)現(xiàn),凡是按照該標(biāo)準(zhǔn)執(zhí)行試驗,若產(chǎn)品出現(xiàn)裂紋而不進(jìn)行改進(jìn)設(shè)計,直接進(jìn)入量產(chǎn),在市場應(yīng)用中存在斷軸召回隱患。
經(jīng)過對大量國內(nèi)外輪轂軸承強度試驗規(guī)范的系統(tǒng)分析,大部分車企均在執(zhí)行SAE J175或GB/T 15704的沖擊試驗標(biāo)準(zhǔn),但也有部分車企并沒有認(rèn)識到這個試驗的重要性,而是通過靜態(tài)壓力試驗評估輪轂軸承的靜強度。實際的車輪上并不存在靜態(tài)緩慢加載的工況條件,車輪在路面上的全程工作狀態(tài)均為動態(tài)承載作用,靜壓試驗并不能替代沖擊試驗。相反,由于駕駛員操作不當(dāng)導(dǎo)致車輪與路面障礙物發(fā)生正向或側(cè)向沖擊的現(xiàn)象倒是屢見不鮮。部分車企僅進(jìn)行靜壓試驗評估而不進(jìn)行沖擊試驗論證就上市車輛,導(dǎo)致斷軸事故層出不窮,最終召回車輛整改。因此,沖擊強度試驗是輪轂軸承開發(fā)過程必做的一項試驗。
2.7 路肩沖擊試驗方法
輪轂軸承路肩沖擊試驗的目的是評估輪轂軸承在路肩撞擊載荷作用下的滾道抗塑性變形能力。路肩沖擊試驗方法起源于質(zhì)量工程師統(tǒng)計發(fā)現(xiàn)輪轂軸承售后失效中滾道等間距布氏壓痕失效模式的比例非常高,從而初步確定了該失效工況。最早對路肩沖擊試驗方法進(jìn)行研究的是美國通用汽車實驗室,其系統(tǒng)研究了輪胎扁平率、氣壓、車輪直徑等因素對沖擊壓痕的貢獻(xiàn)度,在實驗室通過加速器對車輪撞擊復(fù)現(xiàn)了路況沖擊特征,形成了自己的企業(yè)試驗規(guī)范并已應(yīng)用于輪轂軸承產(chǎn)品的開發(fā)。
近年來,萬向精工聯(lián)合大眾、通用開展了路肩沖擊試驗方法的多角度深入研究,研究內(nèi)容包括:
1)通過0.9g~1.5g 外部側(cè)向載荷對滾道壓痕形態(tài)的試驗獲得沖擊工況接觸橢圓與滾道擋邊的比例關(guān)系;
2)通過應(yīng)變式傳感器對實車路肩沖擊載荷進(jìn)行標(biāo)定測試,獲得不同速度下路肩沖擊的實際載荷,為擬定試驗標(biāo)準(zhǔn)提供重要支撐;
3)不同沖擊強度載荷與接觸應(yīng)力的函數(shù)關(guān)系;
4)輪轂軸承沖擊強度對行車噪聲、輪端剛度、輪轂軸承壽命的影響規(guī)律;
5)壓痕深度的量化測量與評估方法。
最終,萬向精工形成了自己的企業(yè)技術(shù)規(guī)范并已應(yīng)用于抗路肩沖擊型產(chǎn)品的研發(fā),該技術(shù)規(guī)范中路肩沖擊的某個沖擊載荷模擬曲線如圖10所示,以2 kN/s的加載速率作用于車輪半徑處,達(dá)到峰值載荷并保壓1 s后瞬間釋放。
圖10 路肩沖擊試驗方法載荷動作圖
Fig.10 Loading diagram of road shoulder impact test method
2.8 力矩剛性試驗方法
輪轂軸承力矩剛性試驗的目的是評估輪轂軸承在承受車輪彎矩條件下的角剛度。力矩剛性試驗方法相對較簡單,在輪轂軸承車輪半徑處以緩慢速率施加軸向載荷,同步在輪轂軸承的凸緣與外圈零件上分別設(shè)置位移傳感器以獲取其相對角度變化,最終獲得力矩剛性。
力矩剛性試驗執(zhí)行過程中需要重點關(guān)注2個試驗細(xì)節(jié):
1)安裝方位對力矩剛性的影響,軸向加載方向與輪轂軸承外圈安裝方位之間的相對位置關(guān)系(圖11)對力矩剛性試驗結(jié)果存在很大的影響,該安裝位置差異對剛性的影響幅度達(dá)到了20%,這是車輪安裝方位設(shè)計需要考慮的因素;
2)輪轂軸承內(nèi)部類似于背靠背雙列角接觸球軸承的結(jié)構(gòu)形式,鋼球分布與軸向加載方向相對位置關(guān)系是隨機的,該隨機性帶來的力矩剛性測量差異約為5%。
圖11 剛性試驗中凸緣外圈的3種布置方位
Fig.11 Three kinds of arrangements of flange outer ring in stiffness test
目前,大多數(shù)車企均在追求高剛度的輪端以提高乘用車的駕駛操控性,一些車企對輪轂軸承單元的力矩剛性設(shè)計要求只給出了下限,而馬自達(dá)輪轂軸承設(shè)計規(guī)范與圖紙則明確規(guī)定了力矩剛性設(shè)計要求的上、下限。筆者認(rèn)為一個更科學(xué)合理的設(shè)計應(yīng)參考馬自達(dá)的設(shè)計思路,在保證乘用車駕駛操控性的同時,應(yīng)避免過高剛度而犧牲了乘坐舒適性。
2.9 微動磨損試驗方法
輪轂軸承微動磨損試驗的目的是評估輪轂軸承滾道抗微動磨損的能力。微動磨損試驗方法同樣起源于質(zhì)量工程師的統(tǒng)計分析,其發(fā)現(xiàn)輪轂軸承售后失效中滾道等間距偽布氏壓痕失效模式的比例非常高,從而初步確定了該失效工況。輪轂軸承隨整車一起從總裝車間下線前往各大城市4S店的運輸路途中(圖12),因路面的低頻顛簸而引起軸承滾道發(fā)生微動磨損,導(dǎo)致售出車輛因磨損缺陷在道路行駛中產(chǎn)生異響。
圖12 乘用車的運輸過程
Fig.12 Transportation process of passenger car
微動磨損而引起的輪轂軸承滾道磨損形態(tài)及圓度儀檢測結(jié)果如圖13所示,磨損表現(xiàn)出2個特征:等間距磨斑;磨斑呈現(xiàn)棕黃色高溫跡象。
圖13 滾道微動磨損形態(tài)圖
Fig.13 Fretting wear morphology of raceway
對微動磨損試驗方法的研究最早出現(xiàn)在日系車企,并在2008年前后形成了各自的微動磨損試驗標(biāo)準(zhǔn),在常溫與低溫環(huán)境下,對輪轂軸承施加4 Hz以內(nèi)低頻等相位的徑向載荷與軸向載荷,然后拆解樣品并評判其滾道的磨損深度。日本鷺宮制作所率先研制了帶環(huán)境箱的兩軸微動磨損試驗臺。2013年,通用也開發(fā)了自己的試驗方法,同樣對輪轂軸承施加4 Hz以內(nèi)的低頻徑向載荷與軸向載荷,但采用了異步相位載荷,疊加彎矩載荷比日系車企更加苛刻。2017年,德國一些車企與德國布倫瑞克大學(xué)合作研究微動磨損發(fā)生機理,研制了三軸微動磨損試驗系統(tǒng)并引入了環(huán)境箱以滿足低溫條件下的試驗。相比日系與美系車企,其增加了一個擺角工況(擺角頻率一般在1 Hz以內(nèi)),以模擬運輸過程中的切向擺動。
2.10 其他功能試驗方法
輪轂軸承功能性試驗相對較簡單,一般為靜態(tài)性試驗,主要包括:
1)凸緣螺栓牢固性試驗;
2)磁性圈磨損試驗;
3)動平衡試驗;
4)靜態(tài)氣密性試驗;
5)環(huán)境腐蝕試驗。
這些試驗主要集中在國內(nèi)車企、美系車企及日系車企,車企執(zhí)行該試驗的目的是對性能試驗進(jìn)行補充,但其實大部分功能試驗均可以在性能試驗中得到復(fù)現(xiàn),例如:螺栓牢固性試驗在耐久性試驗中已被綜合評價,靜態(tài)氣密性試驗和環(huán)境腐蝕試驗在密封試驗中被評價。重復(fù)驗證保證了產(chǎn)品的可靠性,但增加了產(chǎn)品開發(fā)周期與開發(fā)成本。
3、性能試驗方法研究展望
據(jù)不完全統(tǒng)計,目前全球輪轂軸承性能試驗方法標(biāo)準(zhǔn)達(dá)上百種,且不同客戶間的差異很大。各大知名主機廠與輪轂軸承制造商的輪轂軸承性能試驗方法各有所長,但對于一個輪轂軸承制造商而言,同時開發(fā)多個主機客戶的項目就必須配備不同的試驗系統(tǒng),難以將多個客戶的性能試驗方法融合到一個試驗臺上。顯然,這不利于行業(yè)進(jìn)步,建議由國家或汽車行業(yè)牽頭,集各主機廠的長處,制定科學(xué)合理的試驗標(biāo)準(zhǔn),打破不同車企的隔閡,實現(xiàn)在同一試驗標(biāo)準(zhǔn)平臺下的設(shè)計對標(biāo)與評判,以降低輪轂軸承制造商的產(chǎn)品開發(fā)成本,縮短產(chǎn)品開發(fā)周期,提升市場競爭力。
(來源:軸承雜志社)
軸研所公眾號 軸承雜志社公眾號
營銷熱線
0379-64367521
0379-64880626
13693806700
0379-64880057
0379-64881181